FALLSTUDIE
Implementierung von 3D-Messungen zur Qualitätskontrolle in der Automobilindustrie
Die Automobilindustrie steht unter dem ständigen Druck, qualitativ hochwertige Fahrzeuge zu produzieren und gleichzeitig effizient und wirtschaftlich zu sein. Die Gewährleistung von Genauigkeit und Präzision bei den Komponenten ist unerlässlich, um Sicherheitsstandards und Kundenerwartungen zu erfüllen.
In dieser Fallstudie untersuchen wir, wie ein führender Automobilhersteller erfolgreich 3D-Messtechnik implementiert hat, um seine Qualitätskontrollprozesse zu verbessern.
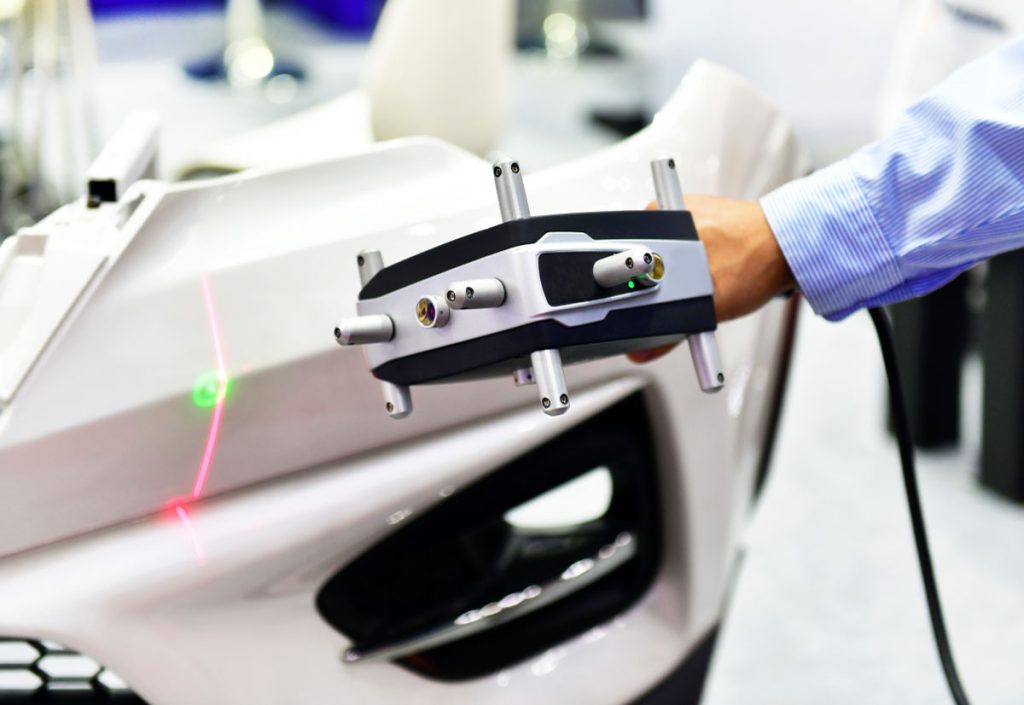
Aufgabenstellung
Das Unternehmen erkannte die Notwendigkeit, die Qualitätskontrolle der Komponenten in seinem Herstellungsprozess zu verbessern. Die bestehenden Qualitätskontrollmethoden stützten sich in großem Maße auf manuelle Messungen mit herkömmlichen Messgeräten und Werkzeugen. Dieser Ansatz war zeitaufwändig, anfällig für menschliche Fehler und in Bezug auf die umfassende Bewertung komplexer Komponenten begrenzt. Um seinen Wettbewerbsvorteil zu erhalten, benötigte das Unternehmen eine Lösung, die Folgendes bieten kann:
- Steigerung der Messgenauigkeit.
- Verkürzung der Messzeit zur Steigerung der Produktionseffizienz.
- Bereitstellung umfassender Daten für tiefgreifende Analysen und Prozessverbesserungen.
- Sicherstellung der Einhaltung von Branchenvorschriften und Sicherheitsnormen.
- Verringerung von Mess-/Kontrollfehlern
Kundenprofil
Branche: Automobilindustrie
Größe: 1.000+ Mitarbeiter
Produkte: verschiedene Pkw-Modelle
Die Lösung
Nach einer gründlichen Auswertung und Konsultationen mit unseren Fachleuten für 3D-Messtechnik entschied sich das Unternehmen für die Einführung eines hochmodernen 3D-Messsystems in seinen Produktionsanlagen. Die gewählte Lösung umfasste folgende Komponenten:
Hochpräzise 3D-Scanner: Wir haben hochpräzise 3D-Scanner an kritischen Stellen in unserem Produktionsprozess installiert. Diese Scanner nutzen Lasertechnologie, um detaillierte dreidimensionale Bauteildaten zu erfassen.
Software für die 3D-Messtechnik: Für die Verarbeitung der gescannten Daten wurde eine spezielle 3D-Messsoftware verwendet. Diese Software ermöglichte das präzise Messen, Ausrichten und Vergleichen von gescannten Bauteilen mit digitalen CAD-Modellen.
Integriertes Datenmanagement: Wir haben Daten aus 3D-Messungen in unsere bestehenden Qualitätsmanagementsysteme integriert. Dies ermöglichte eine reibungslose gemeinsame Nutzung und Analyse von Daten zwischen verschiedenen Abteilungen, von der Konstruktion und Entwicklung bis zur Produktion und Qualitätskontrolle.
Aus- und Weiterbildung der Arbeitskräfte: Es wurde ein umfassendes Schulungsprogramm eingeführt, um sicherzustellen, dass die Mitarbeiter in der Lage sind, die neue Technologie zu nutzen. Dazu gehörten technische Schulungen zu den Geräten und der Software sowie die Integration von 3D-Messkonzepten in die Qualitätskontrollverfahren des Unternehmens.
Der Implementierungsprozess
Der Implementierungsprozess erfolgte in mehreren Phasen, um Produktionsunterbrechungen zu minimieren:
Pilot Phase: Wir führten ein Pilotprojekt in einer ihrer Produktionsstätten durch. Diese Phase umfasste die Installation von 3D-Messgeräten, die Schulung der Mitarbeiter und die Erprobung der Technologie in kleinem Maßstab, um sicherzustellen, dass die Anforderungen des Unternehmens erfüllt wurden.
Phase der Inbetriebnahme: Nach einer erfolgreichen Pilotphase führten wir die Technologie schrittweise in allen Produktionsstätten ein. Dazu gehörten die Installation weiterer 3D-Scanner, die Ausweitung des Schulungsprogramms für die Mitarbeiter und die unternehmensweite Integration des Datenmanagementsystems.
Kontinuierliche Verbesserung: Sie überprüften und verbesserten ihre Qualitätskontrollprozesse regelmäßig auf der Grundlage der vom 3D-Messsystem generierten Daten. Dieser iterative Ansatz ermöglichte es ihnen, Anpassungen an den Fertigungsprozessen in Echtzeit vorzunehmen und ein höheres Maß an Qualität und Effizienz zu erreichen.
Ergebnisse
Die Implementierung der 3D-Messtechnik hat dem Unternehmen erhebliche Verbesserungen gebracht:
Verbesserte Präzision: Das 3D-Messsystem lieferte Messungen mit einer Genauigkeit im Submillimeterbereich, wodurch die Fehlerwahrscheinlichkeit reduziert und die Einhaltung der strengen Industrietoleranzen gewährleistet wurde.
Gesteigerte Effizienz: Die Messzeit wurde im Vergleich zu manuellen Methoden erheblich reduziert, was zu schnelleren Produktionszyklen und höherer Produktivität führt.
Datengestützte Entscheidungsfindung: Daten aus 3D-Messungen sind zu einer wertvollen Informationsquelle für die Gesellschaft geworden. Sie ermöglichten es, Trends, Abweichungen und Verbesserungspotenziale in den Produktionsprozessen zu erkennen, was zur Senkung der Produktionsfehlerquote führte.
Einhaltung von Vorschriften: Die Fähigkeit des Unternehmens, Qualitätsstandards und Sicherheitsvorschriften konsequent einzuhalten, hat sich verbessert, wodurch das Risiko kostspieliger Produktrückrufe und Bußgelder verringert wurde.
Wettbewerbsvorteil: Die Einführung der 3D-Messtechnik hat dazu beigetragen, dass das Unternehmen seinen Ruf als Hersteller hochwertiger Fahrzeuge gefestigt und dadurch seine Wettbewerbsfähigkeit auf dem Markt gesteigert hat.
Fazit
Die Einführung der 3D-Messtechnik hat die Prozesse der Qualitätskontrolle im Unternehmen revolutioniert. Durch den Einsatz von hochpräzisen 3D-Scannern, fortschrittlicher Messsoftware und integriertem Datenmanagement erreichte man ein höheres Maß an Genauigkeit, Effizienz und Einhaltung von Industriestandards.
Diese Fallstudie zeigt, wie die Einführung innovativer Technologien zu erheblichen Verbesserungen in der Qualitätskontrolle führen kann, von denen letztendlich sowohl das Unternehmen als auch seine Kunden in der Automobilindustrie profitieren.